Bulk Material Characteristics
Use these definitions to interpret the nature of your bulk material.
Maximum Particle and Bulk Material Lump Size
Particle size can be quantified in inches or by a mesh screen gauge. Other designations for material size, such as irregular, shredded, or percentage of oil, require special attention during the design process. Alongside particle size, the size of lumps is also a critical factor.
Bulk Density
The conveying capacity of screw conveyors and feeders is measured volumetrically in cubic feet per hour (ft³/hr). To convert capacities from tons per hour or pounds per hour to cubic feet per hour, the bulk density of the material must be known.
The Bulk Material Table's bulk density column offers either an average bulk density or a density range for each material. Precise bulk density data is crucial for the correct selection of a screw conveyor or feeder.
% Trough Loading
Trough loading is a key determinant of conveyor size and depends on the maximum depth that bulk materials can flow through a screw conveyor without excessive wear on components like screws, hanger bearings, coupling shafts, and troughs. It is advised to use a lower trough loading for abrasive bulk materials than for non-abrasive ones.
Each of these characteristics affect how the material reacts to and moves through the conveyor.
Each of these characteristics affect how the material reacts to and moves through the conveyor.
Abrasiveness, Corrosiveness, Flowability & Special Characteristics
Each of these characteristics affect how the material reacts to and moves through the conveyor.
The characteristics explanations and the Bulk Material Table on the following pages contain important information for the proper design of screw conveyors and screw feeders.
Bulk Material Lump Size
When designing a conveying system, the lump size of the bulk material must be taken into account. The diameter of a screw conveyor is influenced not only by the material's capacity but also by the size and proportion of lumps within it. The lump size is defined by the largest lump's maximum dimension. If a lump's length significantly exceeds its transverse cross-section, this longer dimension should be used to define the lump size.
When designing a screw conveyor, the nature of the lumps should be taken into account. Some bulk materials contain hard lumps that do not disintegrate during conveyance. Conversely, other materials may possess lumps that, while relatively hard, tend to break down during conveyance, leading to a decrease in lump size. For bulk materials with lumps that disintegrate easily during conveyance, there are no restrictions on the size of the conveyor.
The permissible size of a lump in a screw conveyor depends on the radial clearance between the center pipe's outside diameter and the trough's inside radius, as well as the lump proportion in the mixture. The conveyor should transport the lumps without obstructing the flow of bulk material or causing damage. Lumps need to fit within the clearance between the trough's interior and the center pipe. Radial clearance details are provided below.
Bulk Material Lump Classification
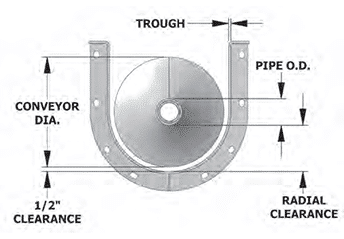
Bulk materials are categorized according to the percentage of lumps present in the overall mixture.
Class 1
Class 1 bulk materials consist of a blend of lumps and fines, where a maximum of 10 percent are lumps ranging from the largest size to half of that size, and 90 percent are lumps smaller than half of the maximum size.
Class 2
Class 2 bulk materials consist of a mix of lumps and fines, with no more than 25% being lumps ranging from the maximum size to half of that maximum size, and 75% being lumps smaller than half of the maximum size.
Class 3
Class 3 bulk materials consist of a mixture where no more than 95% are lumps ranging from the maximum size to half of that, and 5% are smaller than half the maximum size.
Lump Size Ratio
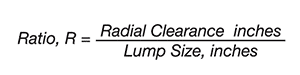
Lump Size Ratio (R) is a function of screw conveyor radial clearance and lump size. The ratio is used to determine the correct screw conveyor design based on maximum bulk material lump size.
Bulk Material Lump Size Table
Screw Dia. | Pipe Size | Pipe O.D. | Radial Clearance | Class 1 (R = 1.75) |
Class 2 (R = 2.5) |
Class 3 (R = 4.5) |
---|---|---|---|---|---|---|
4” | 1-1/4” | 1-5/8” | 1-11/16” | 3/4” | 1/2” | 1/4” |
6” | 2” | 2-3/8” | 2-5/16” | 1-1/4” | 3/4” | 1/2” |
9” | 2” | 2-3/8” | 3-13/16” | 2” | 1-1/2” | 3/4” |
2-1/2” | 2-7/8” | 3-9/19” | 2” | 1-1/4” | 3/4” | |
12” | 2-1/2” | 2-7/8” | 5-1/16” | 2-3/4” | 2” | 1” |
”3 | 3-1/2” | 4-3/4” | 2-1/2” | 1-3/4” | 1” | |
3-1/2” | 4” | 4-1/2” | 2-1/2” | 1-3/4” | 3/4” | |
14” | 3” | 3-1/2” | 5-3/4” | 3-1/4” | 2-1/4” | 1-1/4” |
3-1/2” | 4” | 5-1/2” | 3” | 2” | 1” | |
16” | 3-1/2” | 4” | 6-1/2” | 3-1/2” | 2-1/2” | 1-1/4” |
4” | 4-1/2” | 6-1/4” | 3-1/2” | 2-1/4” | 1-1/4” | |
18” | 3-1/2” | 4” | 7-1/2” | 4-1/4” | 2-3/4” | 1-1/2” |
4” | 4-1/2” | 7-1/4” | 4” | 2-3/4” | 1-1/2” | |
20” | 3-1/2” | 4” | 8-1/2” | 4-3/4” | 3-1/4” | 1-3/4” |
4” | 4-1/2” | 8-1/4” | 4-1/2” | 3-1/4” | 1-3/4” | |
24” | 4” | 4-1/2” | 10-1/4” | 5-3/4” | 4” | 2-1/4” |
30” | 5” | 5-9/16” | 12-11/16” | 7” | 5” | 2-3/4” |
36” | 6” | 6-5/8” | 15-3/16” | 8-1/2” | 6” | 3-1/4” |
Trough Loading
Trough loading refers to the depth of bulk material in a screw conveyor's trough, expressed as a percentage of a full trough, which is 100-percent full. Recommended trough loadings of 15, 30, and 45 percent are established based on bulk material characteristics. The appropriate trough loading for a screw conveyor depends on the material's density, abrasiveness, and flowability. The size and speed of the screw conveyor for a specified capacity are dictated by the trough loading percentage.
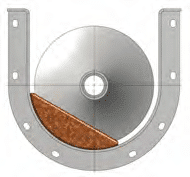
15% Trough Loading
Conveying bulk materials with a density range of 50 to 120 lbs/ft^3, which are highly abrasive and sluggish like alumina, glass cullet, or potash, can be challenging as they do not flow smoothly through a screw conveyor. It is essential to maintain the trough loading significantly below the center pipe to minimize excessive wear on conveyor parts, including screws, hanger bearings, coupling shafts, and troughs. For bulk materials of similar properties, a trough loading of 15 percent is advised.
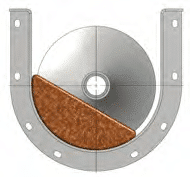
30%A Trough Loading
Bulk materials that have a density range from 15 to 60 lbs/ft3 and are mildly abrasive and free-flowing, such as carbon black, fish meal, or spent brewer's grain, can be conveyed through a screw conveyor. The trough loading may be increased to just below the center pipe level without causing excessive wear on conveyor components like screws, hanger bearings, coupling shafts, and troughs. For bulk materials with similar properties, a trough loading of 30 percent is recommended.
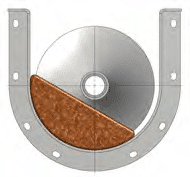
30%B Trough Loading
Bulk materials that have a density range of 30 to 80 lbs/ft3, are highly abrasive, and possess average flowability, such as crushed bauxite, cement clinker, or flue dust, pose challenges in conveyance and do not flow smoothly through a screw conveyor. It is possible to increase the trough loading to just below the center pipe level without excessively wearing out conveyor components like screws, hanger bearings, couplings, shafts, and troughs. For bulk materials with similar properties, a 30-percent trough loading is advisable. When handling materials with a 30B trough loading, the screw conveyor's speed should be decreased compared to materials with a 30A trough loading.
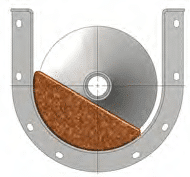
45% Trough Loading
Bulk materials that are non-abrasive and highly free-flowing, with a density range of 5 to 40 lbs/ft3, like alfalfa, baking soda, or hulled rice, can easily pass through a screw conveyor. It is possible to increase the trough loading up to the level of the center pipe without excessive wear on conveyor parts, including screws, hanger bearings, coupling shafts, and troughs. For bulk materials of similar properties, a trough loading of 45 percent is recommended.